News
Saving energy in multi-cavity moulds
Market demands for systems with increasing performance and greater energy savings are becoming increasingly common. However, this concept should not only be limited to energy savings, i.e., low consumption, but should also include waste reduction during the start-up and colour-change phases. The more the cavities are involved, the more evidence of benefits.
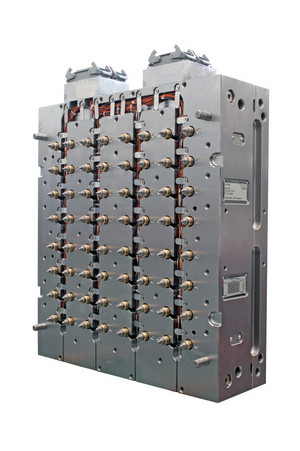
Creating heating solutions with simulations
For this specific case, the HRS Flow Multitech division proposed a solution with MT29-75 nozzles. The part was a yogurt injection mold cap (2 gm, 1.6 mm thickness ) moulded in HDPE. Considering these are systems running at very short cycle times, special attention was given to the thermo-fluid dynamics aspect of the whole system. The hot runners include innovative systems that balance the melt flow in the runner in the most optimal way, the company said.